Servis
Contact Us
Pump Selection
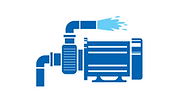
A Guide to Selecting and Designing Industrial Pumps
In the world of industrial operations, the selection and design of pumps are critical steps that can significantly impact efficiency, reliability, and overall performance. Whether it's for transporting fluids, boosting pressure, or maintaining flow rates, choosing the right pump and optimizing its design are essential for achieving desired outcomes. Here's a comprehensive guide to help navigate through the process:
Understanding Requirements:
Fluid Properties: Start by thoroughly understanding the properties of the fluid being pumped, including viscosity, temperature, corrosiveness, and abrasiveness. This knowledge will influence the choice of materials and pump type.
Flow Rate and Pressure: Determine the required flow rate and pressure for the application. This information is crucial for selecting the pump size and capacity.
Operating Conditions: Consider factors such as temperature variations, altitude changes, and potential system fluctuations to ensure the pump operates effectively under all conditions.
Pump Selection:
Types of Pumps: Familiarize yourself with the different types of pumps available, such as centrifugal, positive displacement, and axial flow pumps. Each type has its advantages and limitations based on the application requirements.
Efficiency and Reliability: Look for pumps that offer high efficiency and reliability to minimize energy consumption and maintenance costs over the pump's lifecycle.
Material Selection: Choose pump materials that are compatible with the fluid being handled to prevent corrosion, erosion, or contamination issues.
Sizing and Capacity: Select a pump size and capacity that aligns with the required flow rate and pressure, ensuring optimal performance without overloading the system.
Design Considerations:
Hydraulic Design: Pay attention to the pump's hydraulic design, including impeller shape, casing configuration, and inlet/outlet geometry, to maximize hydraulic efficiency and minimize losses.
Mechanical Design: Evaluate the pump's mechanical design, such as shaft strength, bearing arrangements, and sealing mechanisms, to ensure durability and reliability under operating conditions.
System Integration: Consider how the pump will integrate into the overall system, including piping layout, control mechanisms, and safety features, to optimize system performance and safety.
Energy Efficiency: Incorporate design features that promote energy efficiency, such as variable frequency drives, impeller trimming, and optimized pump curves, to reduce energy consumption and operating costs.
Testing and Validation:
Prototype Testing: Conduct thorough testing of pump prototypes under simulated operating conditions to validate performance, identify potential issues, and fine-tune design parameters.
Quality Assurance: Implement quality assurance measures throughout the manufacturing process to ensure consistent product quality and reliability.
Field Testing: Perform field testing of installed pumps to verify performance in real-world applications and address any operational challenges or optimization opportunities.
Maintenance and Lifecycle Management:
Scheduled Maintenance: Establish a regular maintenance schedule to inspect, lubricate, and replace components as needed to prolong the pump's lifespan and prevent unexpected failures.
Lifecycle Cost Analysis: Conduct lifecycle cost analyses to evaluate the total cost of ownership, including initial purchase price, maintenance expenses, energy consumption, and potential downtime, to make informed decisions about pump selection and operation.
Upgrades and Retrofitting: Consider upgrades or retrofitting options to enhance pump performance, improve efficiency, or adapt to changing operational requirements over time.
By following these guidelines for selecting and designing industrial pumps, you can optimize system performance, maximize reliability, and minimize operational costs for a wide range of industrial applications.